Volkswagen Group is taking electric drive train development and production in-house.
Electric vehicles may be rising in popularity, but they’re still a very small part of total automotive sales worldwide. That being said, car manufacturers can no longer pretend that the EV ‘trend’ is just going to go away. They need to do more to control supply, pricing and development. As such, one of the largest auto conglomerates, Volkswagen Group, just presented an overview of their forthcoming innovations in electric cars.

The focus was on batteries, charging, and electronic components, particularly the electric drive system of the future. Volkswagen has decided to take charge of all essential components, including the development of pulse inverters and thermal management systems, in addition to batteries and electric motors.

A Volkswagen drive system sourced entirely in-house provides considerable efficiency and cost advantages, and the optimal combination of individual components alone could result in up to 20% more efficiency.

Volkswagen’s aim is to become a technology leader, particularly in electric mobility, which is why the company relies on its internal capabilities. After battery cells and electric motors, the company is taking over the development of pulse inverters and thermal management systems. This will make Volkswagen one of the few car manufacturers globally to offer a fully optimised complete system.

The pulse inverter, which serves as the electric drive train’s brain, is responsible for efficiency and performance. Volkswagen has redesigned the hardware and software of the first pulse inverter “designed by Volkswagen” from the ground up. Thanks to the modular toolkit principle, it can be utilised in everything from entry-level engines to sports cars with an output of over 500 kW in the future. The technology is currently being developed for series production maturity and can already be used with the next MEB generation.

Volkswagen is working on entirely new solutions when it comes to thermal management systems. Instead of relying on many individual modules and long hose connections, a compact, integrated thermal module will be used in the future, controlling the entire air conditioning, including for the high-voltage battery. This will have a significant impact on the vehicle’s range and fast-charging capability. The new all-in-one module is also significantly lighter, more robust, and more efficient than current systems.
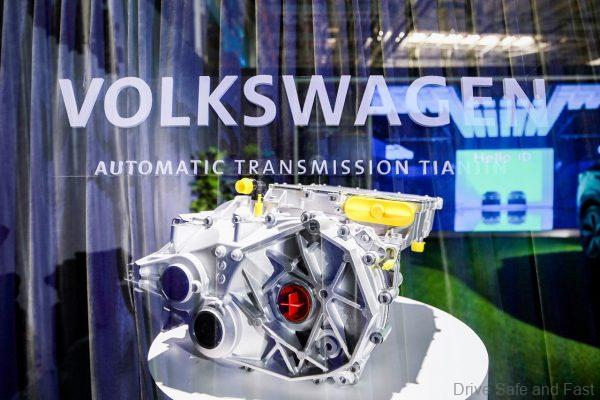
Scalability is the primary focus of the development of all central electric drive components, in addition to efficiency. High economies of scale reduce costs, making Volkswagen more competitive in the industry.

Volkswagen Group Technology consolidates the Group’s activities in batteries, charging, and electric components, acting as a group-wide technology supplier for the brands. Subsidiaries PowerCo (batteries) and Elli (charging and energy) are also involved in the process. The high-tech portfolio includes the unified cell, which will be utilised in all Volkswagen Group vehicles from 2025 and will set a new benchmark in battery technology. The division also includes the Platform Business, which covers collaboration with external partners like Ford and Mahindra. Volkswagen Group Technology employs approximately 70,000 people worldwide.