The Mercedes-AMG ONE Hypercar is now going into production after loads of delays.
Back in 2017, Mercedes-AMG announced their first ever hypercar – the AMG ONE. This was a rather ambitious project as it married Formula 1 technology in a road legal package. However, the company just couldn’t get the car to production in time. It originally was meant to go into production in 2019 but a series of delays set things back a while.
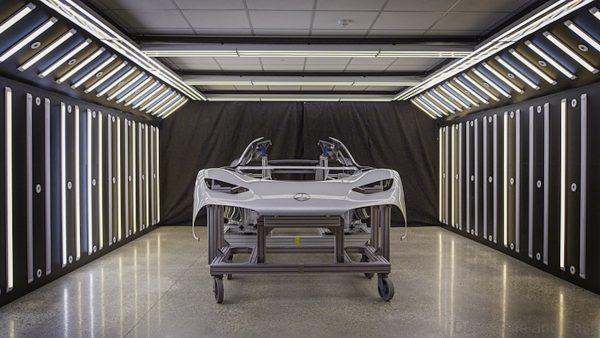
Well it looks like the car is finally going into production. AMG is working with manufacturing partner Multimatic to set up a dedicated small series production facility in the UK.

275 units will be built in total. Each will be hand built at a total of 16 assembly and testing stations.

Learn more about the assembly process of then new Mercedes-AMG ONE below.
PRESS RELEASE
The exclusive car production is completed by hand at a total of 16 assembly and testing stations. Many work steps are reminiscent of the production of high-quality luxury watches: some sub-systems are first pre-assembled and tested for function, then disassembled again and only then finally installed in the vehicle. This applies, for example, to the carbon-fibre monocoque with a bonded-in roof as well as all detachable body parts, which are also made of the light and stable, but also costly material. The entire outer skin is the first to be completely assembled. Now all the fits are meticulously checked and, if necessary, adjusted for size. This is the only way to create a perfectly even joint pattern. In the process, the specialists have to take into account the final lacquering, which adds its own material thickness. Given that the wall thickness of the carbon is only 1.2 millimetres in certain locations, this is a highly difficult and specialised task. Once everything fits together perfectly, parts including doors and bonnets are dismantled again and then hand-painted as a car set for each individual vehicle – this ensures the perfect colour match of the entire vehicle.

In the next assembly step, the powertrain and the body-in-white are assembled: The 1.6-litre V6 turbo engine, the high-voltage battery and the total of four electric machines have all been previously hot tested on testbenches at Brixworth to ensure they are healthy and performant, exactly the same process as is done with Mercedes’ Formula 1 Power Units. Mercedes‑AMG High Performance Powertrains supplies the corresponding units: the eTurbo hybrid combustion engine, the high-voltage battery of the plug-in hybrid, the front axle with the two electric machines and the power electronics including the inverter for each of the four electric motors. In the workflow, 75 percent of the parts are already assembled before the high-voltage components are installed.

A general overview of the production steps organised in 16 main stations:
- Station 1 to 4: Assembly of the mechanical parts and all low-voltage components as well as installation of essential powertrain components including vehicle electrics.
- Station 5 to 6: Assembly of high-voltage battery and high-voltage connections, test runs of combustion engine and electric motors, and commissioning of the vehicle.
- Station 7: Interior Installation.
- Station 8: Start of exterior body panel installation, doors and quarter panels. During this process, the pre-finished body panels; front clam, rear clam, quarter panels and doors, meet the main assembly line from the sub-assembly area of the facility. Here, too, the special challenge lies in the sometimes very different customer wishes.
- Station 9: Continue exterior installation. Front and rear clam.
- Station 10: Final installation of exterior body.
- Station 11: Assembly of wheels and floor panels.
- Station 12: Adjustment of wheels and headlamps.
- Station 13: Roller dynamometer for testing the vehicle in all driving modes.
- Station 14: Four-post NVH test (noise, vibration, harshness), fine-tuning if necessary.
- Station 15: Monsoon rain test.
- Station 16: Light booth with visual inspection of all surfaces and technical function tests of all components.
In total, over 50 specialists work on each individual Mercedes‑AMG ONE. After each station, there are in-depth quality checks based on defined characteristics, resulting in extensive documentation of the production process. The meticulous manufacturing process is complemented by the latest production methods of Industry 4.0, which Mercedes‑AMG also uses at the Affalterbach site for the production of AMG engines. Thus, components are pre-sorted in coordinated sets in material carriers and are available at exactly the right time in the right place.
The final stage of production is marked by a roll-out at a nearby proving ground, where each Mercedes‑AMG ONE undergoes final acceptance testing by a factory test driver. As soon as their approval is given, the vehicle is provided with appropriate transport protection and transported in a closed truck to the Mercedes‑AMG headquarters in Affalterbach. That is where both the technical vehicle briefing by the Mercedes-AMG ONE experts and the handover of the vehicle takes place.