With more EVs and hybrid vehicles on the road, Nissan is studying how to recycle the rare earth elements in electric motors.
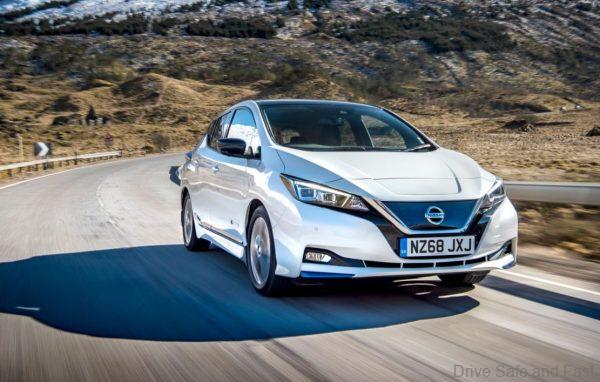
Nissan was one of the first mass-market manufacturer to take on electric vehicles when they made the 1st generation LEAF back in 2010. 11 years later, just about every manufacturer offers at least one battery electric vehicle, with many making bold commitments to transition to electric vehicles completely in the coming years.

This move toward electrification is primarily motivated, or at least marketed, as a push towards sustainability. And to further strengthen the ‘environmental-protection argument for electrification, Nissan is now looking at what to do with the rare earth elements that go into the magnets in many electric motors (but not all).
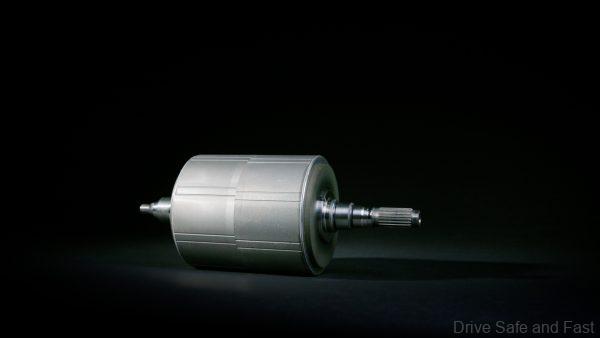
Nissan are working with Waseda University in Japan to develop a recycling process that will efficiently recover high-purity rare-earth elements from these electric motors. Their partnership has been ongoing from 2017 and this year, they co-developed a process of recycling those elements without needing to disassemble the motor. They aim to bring the process to practical and industrial use by the mid-2020s.

Currently, Nissan manually removes magnets with rare-earth elements that do not meet standards to be returned to suppliers. However, with more electric motors making their way into more cars, Nissan is looking for a process that can handle a higher volume of recycling in a more economical process.

Here’s an overview of the process according to the press release.
1. A carburizing material and pig iron are added to the motor, which is then heated to at least 1,400 C and begins to melt.

2. Iron oxide is added to oxidize the REEs in the molten mixture.

3. A small amount of borate-based flux, which is capable of dissolving rare-earth oxides even at low temperatures and highly efficiently recovering REEs, is added to the molten mixture.

4. The molten mixture separates into two liquid layers, with the molten oxide layer(slag) that contains the REEs floating to the top, and the higher density iron-carbon(Fe-C) alloy layer sinking to the bottom.

5. The REEs are then recovered from the slag.

Nissan and Waseda University found that this process was able to recover up to 98% of the rare earth elements in each recycled motor while cutting down the time taken by 50%. The two companies are now working on a way to practically integrate this process in electric vehicle recycling activities. Nissan are also continuing work on their Nissan Green Program 2022 that addresses climate change, resource dependency, air quality and water scarcity with the aim of carbon neutrality and zero new material resource use.