Volkswagen have been on a major electric car offensive with their ‘ID’ family of vehicles. Some cars, like the ID.3 have been met with huge interest from consumers in European markets. However, part of Volkswagen strategy for electrification is to share major electric drive component development and production costs with its partners in China.
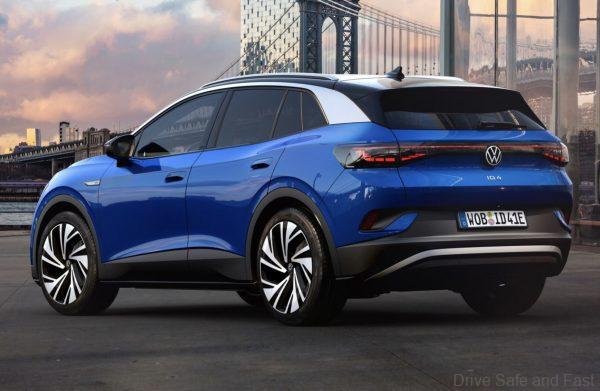
As such, the ‘heart’ of their new ID vehicles, the APP 310 electric drive is now being produced in China along with their existing production line at Kassel. The APP 310 electric drive that’s produced in Tianjin, China will find itse way into Volkswagen ID.4 variants produced by the joint venture partners FAW (ID.4 CROZZ) and SAIC (ID.4 X).
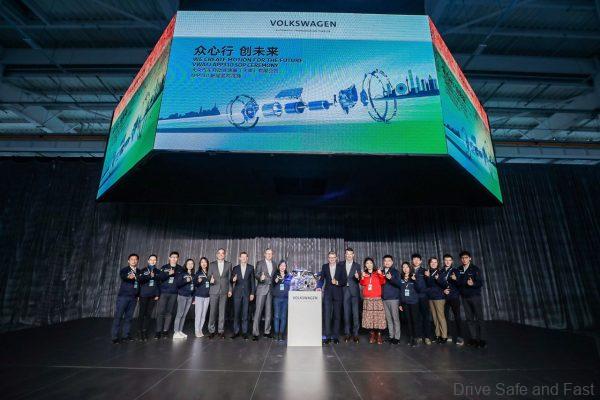
About the APP 310
This drive is a permanent magnet brushless machine. The designation “APP” derives from the arrangement of the drive and the gearbox in parallel with the axle, whilst the numerical sequence that follows derives from the maximum torque of 310 Nm. The main components for this drive are produced using a combination of specialisation and Group manufacturing at various Volkswagen Group Components production sites.
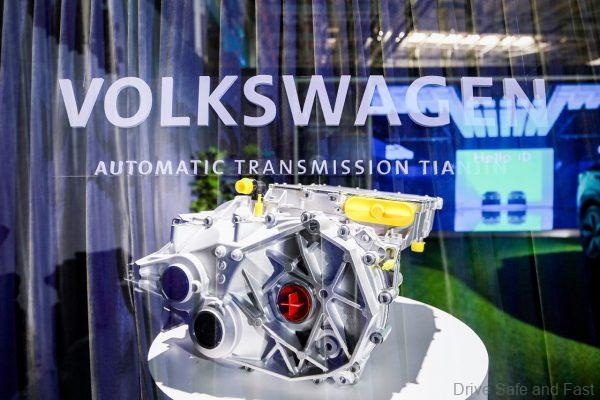
The rotor and stator are produced at the component plant in Salzgitter. New hairpin technology has enabled the use of an innovative production process for the assembly of the stator, whereby the spaces within the laminated core of the stator are optimally filled with flat preformed copper coils. This increases the torque density and the efficiency of the electric drive in comparison to that of a drive with wound copper wire coils. Maximum torque is achieved even at a low engine speed, which means that a 1-speed gearbox is sufficient for the entire rotational speed range. Both the electric drive and the 1-speed gearbox are produced at the component plant in Kassel. The whole drive unit, together with the 1-speed gearbox, is compact enough to fit in a sports bag. The drive weighs only around 90 kg and can generate a peak output of up to 150 kW (204 PS) in the ID.3.
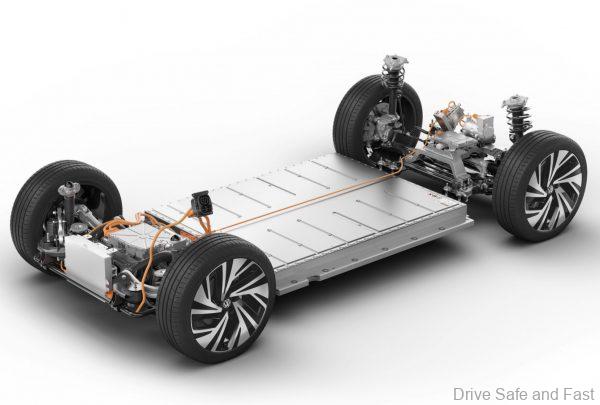
Here’s the press release with more.
PRESS RELEASE
Volkswagen Group Components reinforces its position as a key supplier of central electric vehicle components for the brands and joint ventures of the Volkswagen Group in the most important market for electric mobility. With immediate effect, the Chinese components factory in Tianjin will be producing the APP 310 drive on the modular electric drive matrix (MEB). This component will be used in the Volkswagen ID.401variants produced by the joint venture partners FAW (ID.4 CROZZ02) and SAIC (ID.4 X02). The Group’s future MEB models for China will also be supplied locally. The main factory for electric drives at Volkswagen Group Components in Kassel produces the APP 310 motor for current and future MEB models in Europe and North America.
Automatic gearboxes have been produced at the Tianjin component plant since 2012. Following the ramp-up of the DQ400e hybrid engine and the APP 290 electric drive, the APP 310 represents the next milestone in the transformation to electric mobility. The permanent magnet synchronous machine with the drive and gearbox parallel to the axles has an output of up to 150 kW (204 PS) with a maximum torque of 310 Nm. The two component plants at Kassel and Tianjin are working closely together on the industrialisation process for the new product. At present, the technical capacity installed at both sites corresponds to up to 880,000 electric drives per year. Production is to be expanded by up to 1.4 million electric drives as early as 2023. This would make Volkswagen Group Components one of the largest producers of electric drives in the world.