Volvo has decided that battery packs in its BEVs like the C40 will be developed completely in-house.
Volvo has been pioneering electrification in the premium car game for many years now. They had a fully-electric vehicle, the C30 Electric, on offer as far back as 2011. Of course, the range was not very impressive back in then, the C30 Electric could only do 150km on a full charge, but it was still an important milestone. In the decades since, the company has built the technology up. They introduced Plug-in Hybrid powertrains very early on as top-tier variants of their model lineup, and then completely electrified their entire portfolio.

Now the company has entered a new era of electrification – one led by their new battery electric vehicles (BEVs). BEVs like the C40 are powered by completely different technology from their familiar plug-in hybrid vehicles. In fact, with the XC40 Recharge Pure Electric and the C40 Recharge, Volvo is finally designing and building its own battery packs in-house.
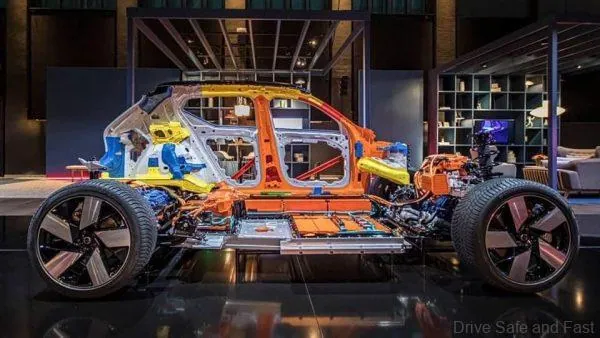
What that means is that there are no shared battery pack components between a Plug-in Hybrid and BEV from Volvo. For their hybrids, Volvo would sign up to long term contracts with suppliers like LG Chem for complete battery systems. Volvo knows that BEVs are much different and it’s important that they bring this knowledge into the company even though it is very much possible to outsource battery pack design for BEVs.

This strategic decision was made because battery packs are the single most expensive component in any electric vehicle and because Volvo does not compromise when it comes to safety. Battery packs play an integral role when it comes to a BEV’s crash structure, but they have to also be designed to protect the cells from short circuiting or from being ruptured. They can do the engineering and testing better when it’s all done in-house.

Speaking of testing, Volvo has its own US$60 million in-house battery testing lab. The work at this facility ensures that batteries that go into BEVs like the C40 can withstand a range of environments, temperatures, currents and types of cycles. Much of testing takes months or even years, as they need to mimic the charge and discharge cycles these lithium-ion cells go through in the real world.
