Last week, before our short test drive of the new Honda City RS e:HEV, we got to take a tour of Honda’s Pegoh Plant in Melaka. The plant actually consists of two Lines. The No.1 Line was established way back in 2003. At the time, Honda Malaysia was still in its early days and were selling fewer than 20,000 units a year through their official channels. When they finally exceeded No.1 Line’s production capacity of 50,000 units a year in 2013, they expanded. By early 2014, No.2 Line was added, beefing up Honda Malaysia’s CKD capacity to 100,000.
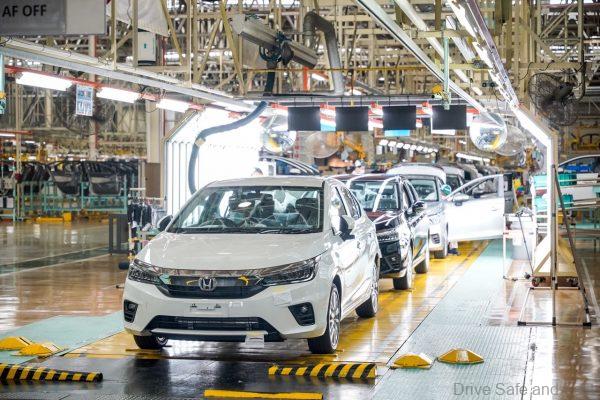
The Pegoh plant is going to be the first in the world to put together the Honda City i-MMD, and that’s no small feat. On the tour, we were shown exactly how the upcoming car is put together from its component parts. Here’s what we learnt along the way.

We’ll start with the chassis, as this is what all buyers of the new City will be interested in (the i-MMD system is only present on the top-spec model). The new City is actually more complex to assemble than most other Hondas in Malaysia right now. The new City’s chassis actually uses an additional ‘inner frame’ for the chassis. Smaller Hondas like the current HR-V, Jazz, and BR-V don’t use this sort of structure, but the larger ones do. This additional layer increases rigidity and makes the new car safer, more refined and better around the corners than its predecessor. Honda Malaysia actually had to purchase 3 new robots for spot welding and insert them into the production line JUST for this new City. All other models bypass this station. Though they didn’t specifically mention this, it’s likely the next generation of the HR-V and Jazz will use this new production method.
As if an inner structure to the chassis isn’t enough, the new City also utilises a new ‘spray foam’ along the floor boards. Honda Malaysia invested in this huge mechanism that blends two elements together at the nozzle that immediately expands and hardens into a rigid sponge material.
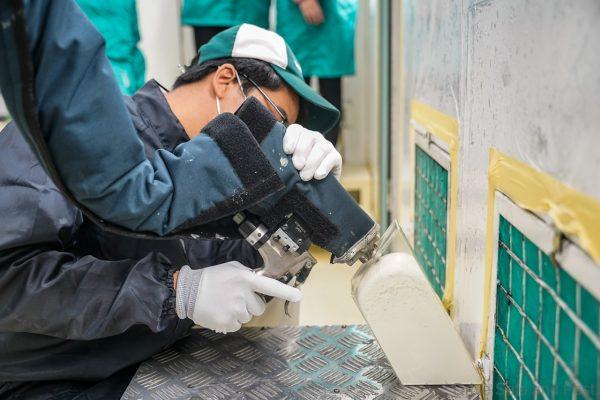
This spray foam material is filled into 6 cavities along the bottom of the A and B pillars of the new City chassis. They fill up these cavities and dampen noise and vibrations resonating from this part of the car.

This new spray foam technique is 33% more effective at improving noise, vibration and harshness characteristics.
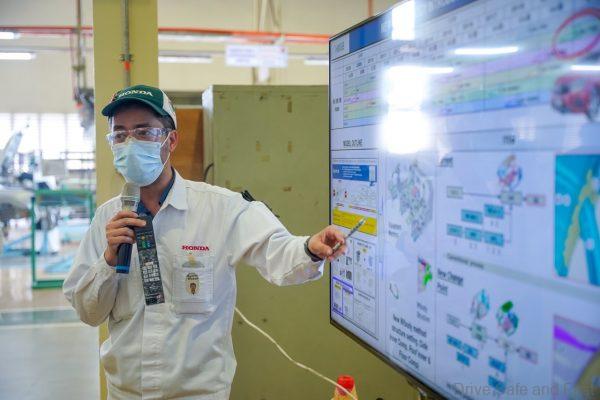
Besides that, the RS models will also benefit from a ‘Variable thickness thinsulate’ sound absorber material that will further improve NVH characteristics over the standard petrol models. Having briefly driven the new Honda City RS, we can actually attest to its quietness compared to its predecessors.
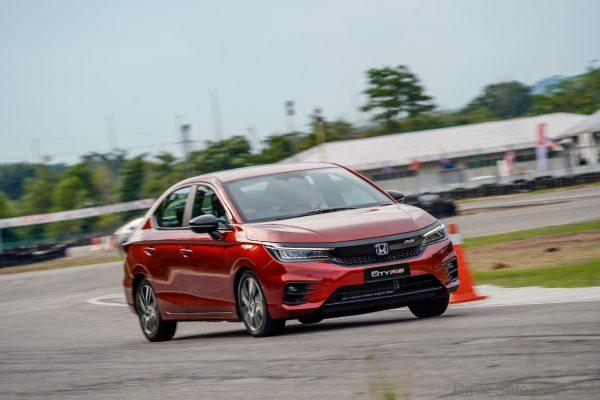
Now that we’re talking about the City RS, we may as well get into the production of the i-MMD system’s components. The engine is completely assembled at the plant in a separate area near No.2 Line. 5 other engines are produced here along with the 1.5-litre DOHC port injected motor that goes into the City RS. The petrol engine is only one part of the equation. Most of the time, the petrol engine will be rotating a generator motor, which converts kinetic energy into electrical energy, which is passed through the Intelligent Power Unit (IPU) at the rear.
The IPU consists of 48 lithium-ion battery cells, split into 4 packs. The job of the IPU is to manage how these batteries are charged, discharged and cooled. The energy recovered is sent to the traction motor at the front to drive the Honda City RS forward and backward, depending on which gear is selected.
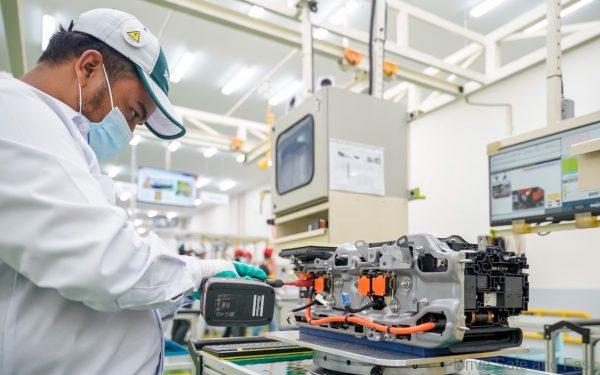
This all important IPU is actually being assembled at Honda’s No.1 Line, in an isolated, air-conditioned room. Here, 6 highly trained associates are in charge of assembling the IPU and they can put together 90 units a day, with each unit taking roughly 2117 seconds to assemble. An IPU weighs 30 kilograms and consists of 50 parts.
The parts come in from suppliers in Japan. There’s a system in place that assist the associates get through the assembly process so that every bolt is torqued to spec and so that the IPU charges and discharges within specification. They also closely monitor the age and temperature of each battery cell brought in from Japan to ensure they’re still factory fresh by the time they’re being assembled in Melaka. This is a very sophisticated production process and production progress is synchronised online to ensure the lithium-ion cells get into fully-assembled IPUs and into customer cars within the stipulated 180 day time frame. The fact that the Melaka plant is the first in the world to assemble IPUs for the new City i-MMD is actually really impressive.

It was our first time taking a tour of the Honda Malaysia Pegoh plant and we got to sample the finished product at the end of the tour. Read about that experience here, or learn more about that new engine from our video below.