The Taycan is now Porsche’s best selling vehicle in their lineup
Porsche may have been a little late to the electric vehicle ‘game’ but they were being cautious as this highly reputable car manufacturer could not have a new technology vehicle returning to their workshops for issues. This is why when the decision to build the Taycan was approved, Porsche product engineers looked at getting the best partners for their first ever full electric production vehicle.

They had to find the best component providers in the business to ensure every Taycan customer gets the Porsche promise of excitement in every single ignition with class best reliability. So, for one of the most important component of any EV today is the battery. This is why Porsche looked at getting the best EV battery supplier to get the best performance. The DRÄXLMAIER Group was picked and they are now working hand in hand with Porsche to deliver high quality battery packs.
The German automobile supplier Dräxlmaier, located near Stuttgart, is starting series production of the 800-volt total battery system for the Porsche Taycan. For this purpose, the Bavarian company built their first battery assembly plant on an area of 10,000 sqm.
The DRÄXLMAIER Group develops and produces vehicle-specific, individually configurable high-voltage battery systems and individual components for high-voltage storage. The DRÄXLMAIER-made E-module includes all vital components, from charging sockets and HV electrical wiring systems, right up to a broad variety of electronic parts that all provide intelligent measuring, distribution and protection, as well as reliable contacting. Like its other products, all battery system solutions are produced in-house at DRÄXLMAIER – from development right up to production.

800-volt system voltage: Less weight, faster charging
The Taycan is the first production vehicle with a system voltage of 800 volts instead of the usual 400 volts for electric cars. This enables consistent high performance, reduces the charging time and decreases the weight and installation space of the cabling.
The two-tier Performance Battery Plus used in the Taycan Turbo S and Taycan Turbo contains 33 cell modules consisting of 12 individual cells each (396 in total). The total capacity is 93.4 kWh. The cells themselves are so-called pouch cells. In this cell type, the stack of electrodes is not enclosed by a rigid housing, but by a flexible composite foil. This allows optimal use to be made of the rectangular space available for the battery and a reduction in weight.

The modules each have an internal control unit for monitoring voltage and temperature and are connected to each other via busbars. The foot garages – recesses in the battery in the rear footwell – provide the best possible seating comfort in the rear and allow the low vehicle height typical of sports cars.
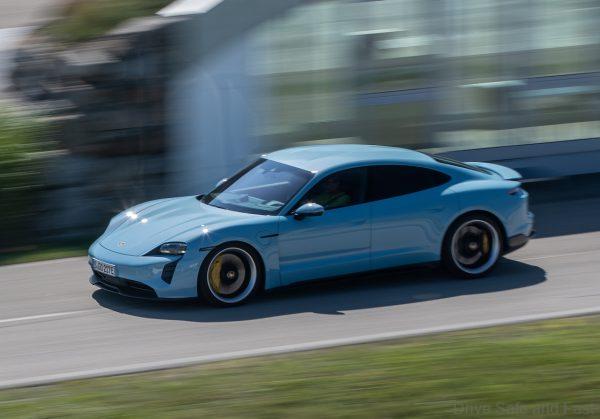
Even more convenient charging
Charging while preserving the battery is a further new function. It can restrict the charging capacity at suitable charging points (e.g. Ionity high-power charging stations) to around 200 kW, when customers are planning to take a longer break from driving. This extends the battery’s service life and reduces the overall power loss. Drivers can select the charging while preserving the battery function on the central display. Of course, if customers choose not to use this option, a charging capacity of up to 270 kW remains available at 800-volt high-power charging stations.
The Dräxlmaier Group got involved in the development of energy storage systems at an early stage in 2009. According to the manufacturer, the first prototypes were soon followed by concept orders for batteries in plug-in vehicles from premium brands.
The Bavarian’s current customer base includes Audi, BMW, Jaguar, Land Rover, Maserati, Mercedes-Benz, Mini, Porsche, VW and several unspecified Californian automakers, one of which is probably Tesla. Founded in 1958, the long-established company employs around 70,000 people at 60 locations in more than 20 countries.