The new Mercedes-AMG A45 and CLA45 will be getting a new M139 engine. This 2-litre direct injection 4 cylinder outputs more power per litre than any other turbocharged engine in series production. But how? Well, here’s the full explanation from Mercedes-AMG.
PRESS RELEASE
Engine design: intelligent details
The new engine excels with numerous intelligent design features. Unlike the likewise transversely installed four-cylinder in the 35 models or the preceding model, the new engine is rotated around its vertical axis by 180 degrees. This means that the turbocharger and the exhaust manifold are now positioned at the rear, on the side of the firewall when viewed from behind. The intake system is therefore positioned at the front. This configuration allows the flattest possible and aerodynamically advantageous front section design. Furthermore, the new arrangement allows much improved air ducting with shorter distances and fewer diversions – both on the intake and exhaust side.

Turbocharger: roller bearings reduce mechanical friction
The new twinscroll turbocharger combines optimum responsiveness at low engine speeds with a high power in the upper rpm range. In addition to this, the turbine housing is divided into two flow passages which run parallel to one another.
Together with the likewise divided ducts in the exhaust manifold, this makes it possible to feed the exhaust flow to the turbine separately. The aim is to prevent the individual cylinders from influencing each other negatively during load cycles, and to improve the gas cycle. The result is higher torque at lower engine speeds, and extremely good responsiveness.
Furthermore, the shafts of the compressor and turbine have roller bearings for the first time ‑ as in the top output variant of the AMG 4.0-litre V8 engine in the AMG GT 4-door Coupé. The roller bearings reduce mechanical friction within the turbocharger to a minimum. The charger therefore responds more readily and reaches its maximum speed of up to 169,000 rpm more rapidly.
Charge pressure: electronically controlled for optimum responsiveness
With a maximum charge pressure of 2.1 bar, the 2.0-litre four-cylinder turbo engine is also the leader in its segment in this respect. The electronically controlled wastegate (exhaust relief valve) allows the charge pressure to be controlled even more precisely and flexibly while optimising responsiveness, especially when accelerating from partial load. Numerous parameters are taken into account in this process. The main input signals for the wastegate control unit are the charge pressure, throttle flap position and the knocking tendency. The modifying signals include the intake air temperature, engine temperature, engine speed and atmospheric pressure. This also makes temporary boosting of the charge pressure (overboost) possible under acceleration.
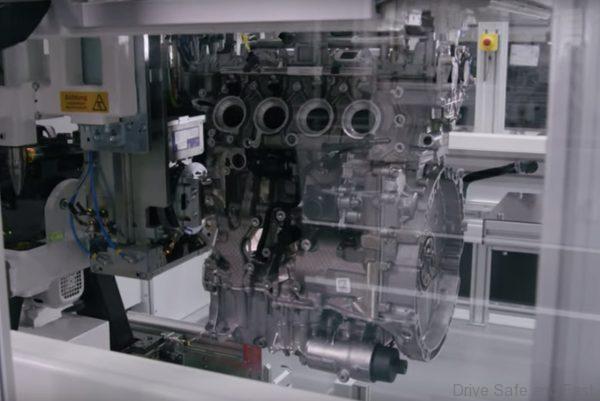
Fresh air is used in addition to oil and water to cool the turbocharger. This is directed specifically to the charger from the radiator grille, via the engine cover designed as an air deflector and ducts beneath the bonnet. The concept is based on the principles and experience gained with the cooling for the internally mounted turbochargers of the current AMG 4.0-litre V8 engines, starting with the AMG GT in 2014. In addition the turbine housing has integral insulation.
Crankcase: all-aluminium with outstanding properties
The all-aluminium crankcase is a chill-cast unit which excels with outstanding material properties. In this process the molten aluminium is poured into the metallic mould using the effect of gravity.
Thanks to its good thermal conductivity, the water-cooled mould allows rapid cooling and solidification of the melt. The result is a fine-grained, dense structure that guarantees very high strength. Complex interior geometries can be realised with the help of enclosed sand cores.

The so-called closed-deck construction – a design taken from motorsport ‑ ensures maximum rigidity with low weight and allows peak combustion pressures of up to 160 bar. The areas around the cylinders are mostly solid, and the cover plate is only penetrated by smaller ducts for the coolant and engine oil. The crank assembly with a lightweight, forged steel crankshaft and forged aluminium pistons with optimised piston rings combines low friction with high strength. The maximum engine speed is 7200 rpm, and peak output is developed at 6750 rpm. The sump features baffle plates so that despite the larger sump, and even under high lateral acceleration forces, there is always sufficient engine oil to lubricate all the relevant components.
Cylinder liners: coated with NANOSLIDE
To reduce friction between the pistons and cylinders, the linings are coated using patented NANOSLIDE technology. This gives the linings a mirror-like surface for minimal friction, is twice as hard as conventional grey cast-iron liners and therefore makes them much more durable. NANOSLIDE was developed by Daimler AG, and is protected by more than 90 patent families and more than 40 patents. This coating was first used in AMG’s M 156 V8 engine, has enhanced other AMG engines for many years and can also be found in the Formula 1 engine of Mercedes AMG Petronas Motorsport.

Exhaust valves: larger dimensions for faster gas cycles
In the cylinder head, the repositioned and slightly angled injection nozzles and spark plug system have allowed much larger exhaust valves than in the preceding engine. The larger exhaust cross-sections allow the gases to stream out of the combustion chambers with low losses, and reduce the overall piston venting action.
Two overhead camshafts control the 16 valves via weight-optimised roller cam followers. Camshaft adjustment on the inlet and outlet side allows an excellent response and optimises the gas cycle for each operating point.
Variable CAMTRONIC valve control on the exhaust side is another feature, with two cams per valve. The cams have different geometries, so that depending on the cam setting to suit the driving situation, the exhaust valves can be opened for short or long periods – for even better responsiveness at low engine speeds, comfortable and fuel-efficient driving at medium rpm and full power delivery in the upper rpm range.

Petrol injection: two stages for optimised power
Turbocharging and direct injection with a spray guided combustion process not only allow a high power yield, but also improve thermodynamic efficiency and therefore reduce both fuel consumption and exhaust emissions.
For the first time, the new high-performance four-cylinder has two-stage fuel injection. In the first stage the particularly fast and precisely operating piezo injectors supply fuel to the combustion chambers at a pressure of up to 200 bar. This is a multiple process at times, and is controlled by the engine management system as required.
In the second stage there is additional intake manifold injection using solenoid valves. This is needed to achieve the engine”s high specific output. The electronically controlled fuel supply has an operating pressure of 6.7 bar.
Cooling: sophisticated system for the engine, turbocharger and charge air
The high output requires an intelligently conceived cooling system. This is so designed that the cylinder head and crankcase can be cooled to different temperature levels. This innovative measure allows a cold cylinder head for maximum output with efficient ignition timing, and a warm crankcase to reduce in-engine friction.
The coolant to the cylinder head is supplied by a mechanical high-performance water pump, while cooling of the crankcase is via a second, electrically driven water pump. After a cold start, this pump remains passive until the engine has warmed up. In operation it is regulated by the engine control unit so that the crankcase is always cooled according to need.
Moreover, the pump can be switched on or off as required when less output is needed, or at low engine speeds. Furthermore, the electric water pump ensures the full engine output and optimum heat dissipation over the entire engine speed range. It also protects against thermal damage when idling in very high ambient temperatures.
In addition the engine has an oil temperature management function which controls the warm-up phase and flexibly regulates the engine oil temperature. This brings the engine to its operating temperature more rapidly, reducing friction and wear. This is accompanied by the environmentally friendly ancillary effect that fuel consumption and cold start emissions are also reduced.

The engine’s high degree of supercharging calls for a high-performance intercooler. So that the charge air can be cooled close to the ambient temperature despite the extreme quantities of heat, for the first time a 2-stage, indirect intercooler has been developed. It works in conjunction with the air conditioning system, and is used in the S-models where it has been integrated into the low-temperature circuit. For this was necessary to completely redesign the configuration of the condenser in the front end. One condenser is located in the wheel arch, and a second one is positioned in first row of the central cooling module. The separate condenser and radiator configuration and thermal management specifically designed to meet (everyday) requirements and (racetrack) performance enable efficient and coordinated cooling performance.
Functions such as alternator management, the ECO start/stop function with fast restarting, the gliding function and a petrol particulate filter are also part of the technology package for the new AMG four-cylinder.
Digital and smart hand assembly: “One man, one engine”
The new engine is entirely assembled by hand. To this end a completely newly designed production line was constructed in the AMG engine manufactory in Affalterbach, where Mercedes-AMG has raised the “One Man, One Engine” principle and Industry 4.0 processes to an innovative level reflecting the latest findings in ergonomics, material flows, quality assurance, sustainability and efficiency. On the road to implementing Industry 4.0, AMG’s hand assembly operation likewise follows the vision of “smart production”.
This excels with maximum flexibility, and is transparent and highly efficient. It safeguards and improves the quality of the engines and production processes using innovative and digital technologies.